YYACHTS YARD
YYachts German shipyard was built for creating sustainable luxury at sea and carbon fibre yachts.
The hub of Michael Schmidt Yachtbau is located on the Baltic Sea on the outskirts of Greifswald, YYachts can produce yachts up to 35 meters LOA. The entire production facility was built from scratch in 2016 in record time and was ready for production in December of that year.
YYachts hulls and rigs are exclusively carbon fibre and use a specially heated paint shop to fully take care of them. Every yacht is tempered, to permanently tight together the multiple layers of carbon fibre and resin to give strength and solidity to the hull. YYachts oven is built to heat up to 90°C degrees so that they are capable of tempering demanding prepregs. Finally, a further step is carried out to perfectly fix the paint. For your yacht, this generally means tempering up to approx. 65 degrees. This gives the entire composite structure a pronounced rigidity and stability which will not shrink even at high temperatures.
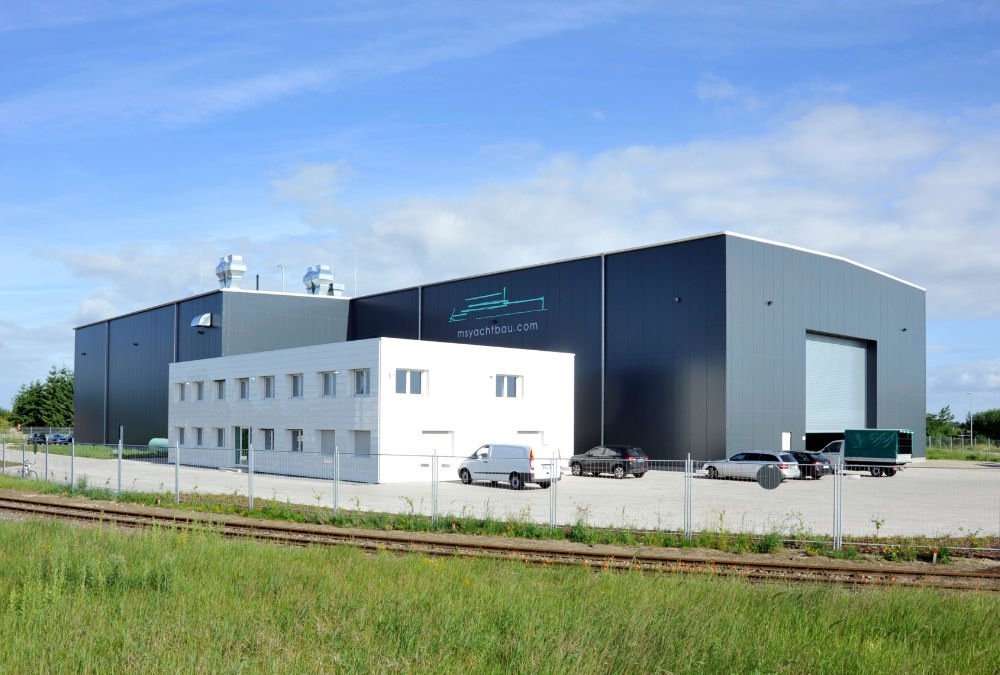
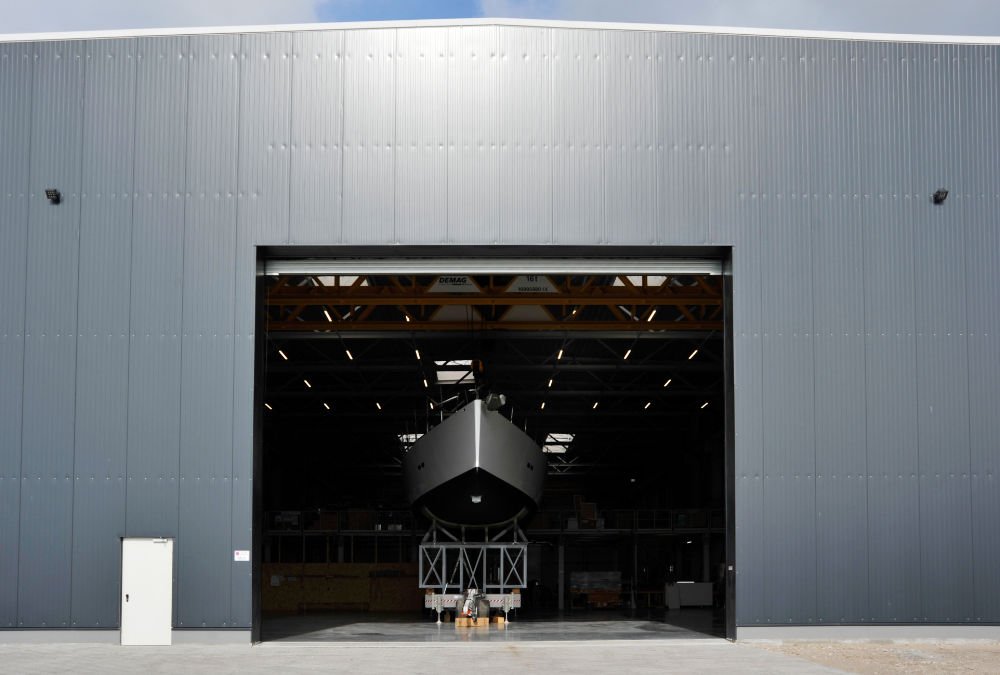
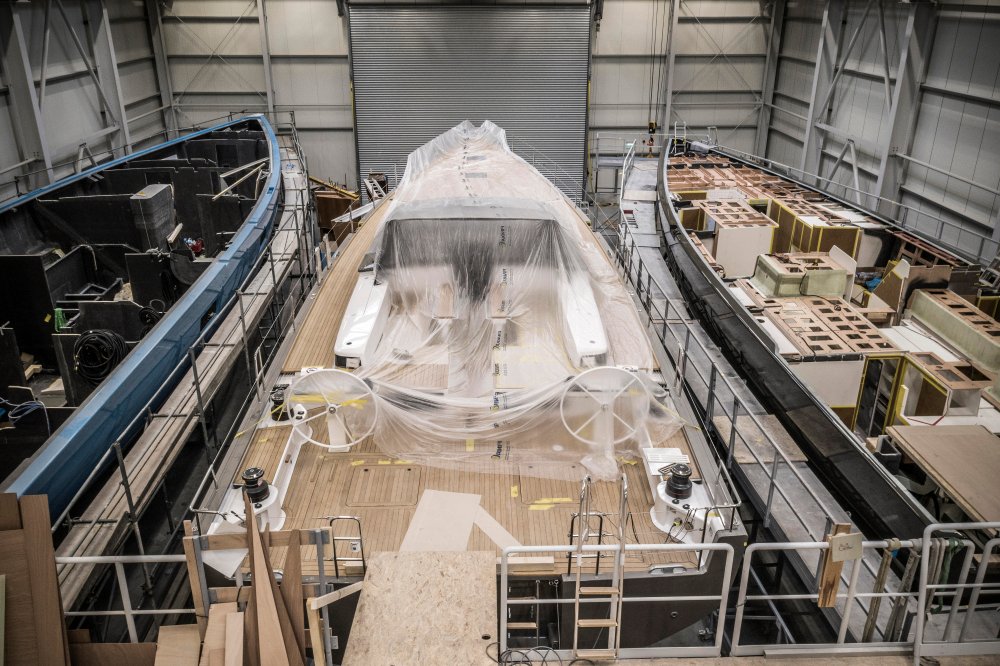
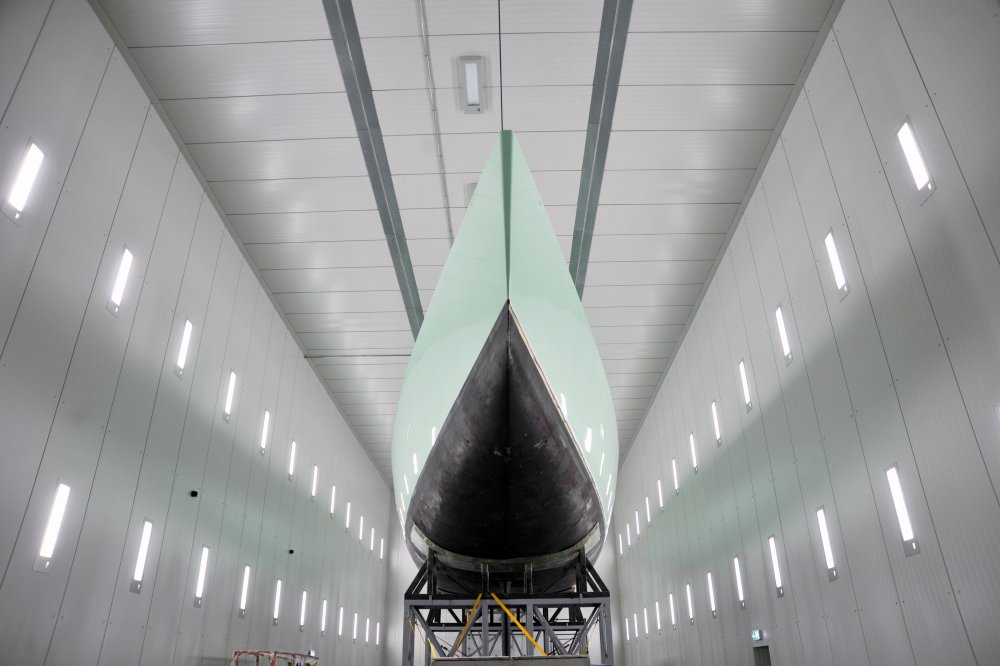
FAST AND EFFICIENT PRODUCTION
In the production process, the various components and internal areas of the boats are built in modular processing to optimize production time, efficiency, and precision of assembly.
For example, the engine room of a YYachts is built in modular construction in parallel with the hull construction. The engine room will already be equipped with all the technical onboard components required by the owner and YYachts technicians. In the assembly phase, the entire preconstructed engine room will be installed in the proper hull space. Only then the thrusters are added and connected by shaft lines or sail drives to the propellers, as well as the electrical cables, pipelines and hydraulics.
This maximizes efficiency and eliminates downtime during production and assembly. Fast and efficient production is possible at the Greifswald production plant thanks to the great skills of employees and a precise organization of carpenters’ work concentrate directly on the projects at hand.
The production of the carbon fibre hulls is outsourced factories in Poland, which work in partnership with YYachts. This allows YYachts to shrink production times, avoiding downtimes.
The production times of Y7 is 6 months, Y8 in 11 months and Y9 is no more than 18 months. In this way, it is not only possible to reduce production time but also to guarantee high-quality standards by relying on leading partner companies.
Once the hull is ready, it is shipped, depending on the model and size, either by truck or by sea using special barges.
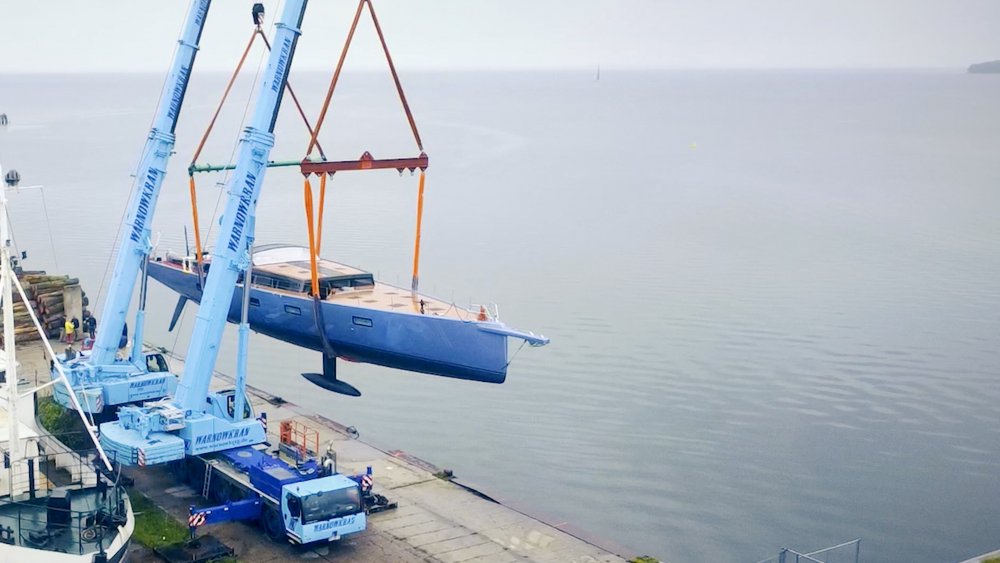
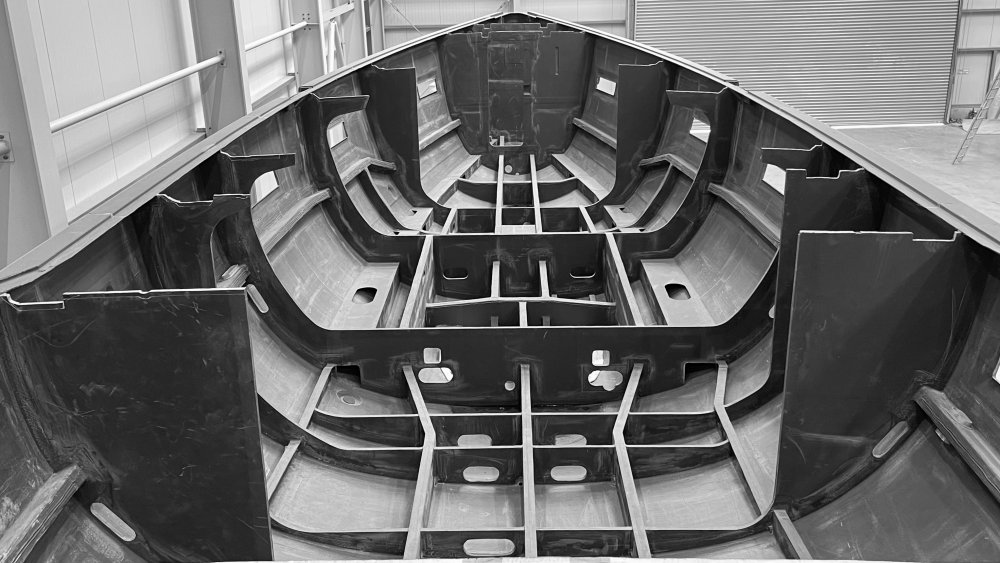
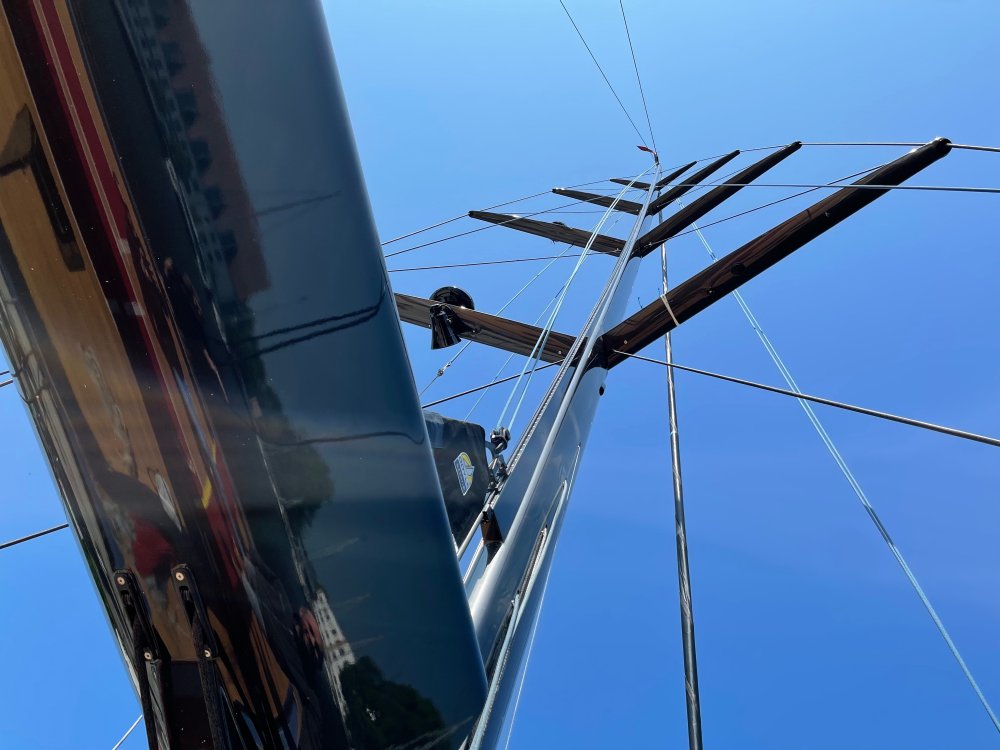
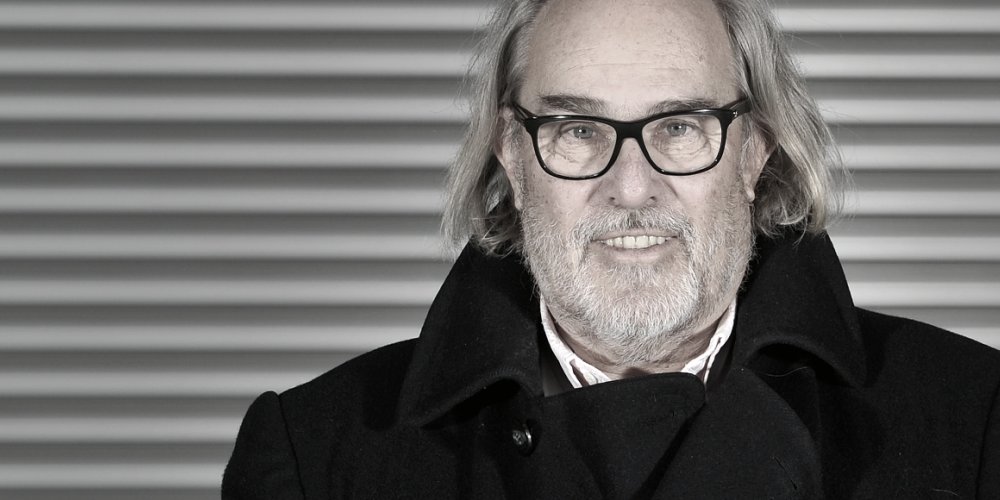
Since the shipyard is no more than 200 meters from the sea, sea transports and in-water operations are facilitated both for hull delivery and launching of the vessels.
In YYachts Yard the assembly of the components takes place, here when raw hulls arrive, they must be processed and finished before being painted. The painting is a rigorous process, the hulls after being levelled are coated by several layers of base and primer to smooth out the surface. Afterwards, an undercoat is applied and on top of it two more layers of topcoat and transparent protective varnish.
Then the internal components of the boat are built below deck, the cabins and the deck itself which will be installed only afterwards. All electrical circuits have to be installed as well as piping, engines and hydraulics.
Once the internal and external structural elements have been completed, the deck is assembled, which has been previously covered with teak or wood chosen by the owner.
Then, the final structure is assembled, the hardware components on the deck are installed, as well as the hydraulic system, and at the same time, our craftsmen build the interiors according to the interior designers’ designs.
Subsequently, the furniture and fittings that the owner has chosen are installed. Only when the interiors are finished, custom-made design décor is set.
The last step is the water launch, which takes place in the waters in front of the yard, here our experts will install the mast and carbon boom fixing it with ultralight rigs.
Usually, the following day, after the carbon cables have been set after tensioning, the rigging is tested first and then a series of meticulous sea trials take place.
Every YYacht is tested by Michael Schmidt himself. He won’t limit to mild tests with little wind but thoroughly tests the boat’s performance. Personally testing the boat’s strength, reliability and behaviour in strong winds. If the boat passes the tests and only after its approval, it can be handed over to the customer with the christening ceremony.